Bin Level Indicators and Inventory Monitoring
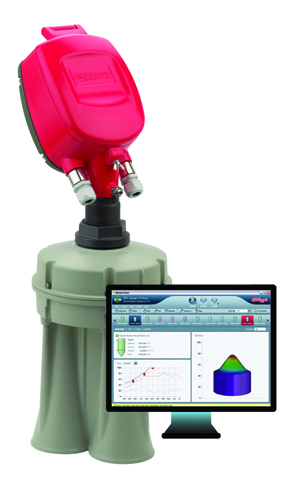
Meeting Material Challenges
Not all materials play nicely. Hog fuel, for example, can behave quite erratically as it’s shredded. Plus, the material can vary in length and tangle together when being conveyed or discharged. When augered into a vessel, hog fuel tends to pile up and clump into oddly shaped forms that are difficult to measure.
As the density of material varies, some non-contact technologies—such as radar—can penetrate the material surface. Pellets tend to be of a consistent size and, when dry, will flow freely, especially in a center-fill, center-discharge vessel. But, sawdust and shavings can be fluffy and light, making it difficult for some level sensing technologies to perform properly due to their low-bulk density. And, due to their irregular shape, wood chips can be difficult to measure. They tend to cling together and don’t flow easily in and out of a bin, particularly if any moisture is present. This can create an irregular material surface, where the level of wood chips vary in one part of the bin compared to another.
If it’s necessary to account for the irregular topography of the material in a bin when monitoring the inventory of wood chips, it is best to measure the level in multiple points in the bin.
Continuous inventory monitoring
Depending on the type of material, the type of sensor used might vary. Here are some guidelines to follow….
Sensor Type |
Sawdust |
Pellets |
Wood chips |
Hog fuel |
3D Acoustic |
|
√ |
√ |
√ |
Cable-based |
√ |
√ |
√ |
√ |
Rotary |
√ |
√ |
√ |
|
Vibrating rod |
√ |
√ |
√ |
|
• Acoustic Scanners
Some facilities prefer non-contact level sensors, since they’re not intrusive and eliminate the risk of becoming encumbered in the tank. A 3D low-frequency acoustic scanner provides the highest level of inventory accuracy by measuring multiple points in a tank and reporting the lowest, the highest, as well as the average level detected. It also reports the estimated volume of material in the tank. Because it operates at a very low frequency, it performs in dust where other non-contact sensors can be inaccurate or unreliable. Although more costly than most single-point measurement devices, it’s the best solution for plants that are looking for increased inventory accuracy.
A 3D acoustic scanner is designed for monitoring and controlling inventory, but isn’t recommended for process control. Rather, it’s used in materials with a bulk density of 12 lb./ft.3 or greater. With its dust-penetrating, multiple-point measurement technology, an acoustic scanner can measure the irregular material surface, and account for the build-up of material in a tank. By measuring multiple points, it can accurately estimate the volume of material in a tank, and can account for the steep angle of repose that occurs frequently in tanks containing woody biomass.
Biomass plants have successfully applied a single 3D acoustic scanner in bins, tanks, and silos containing woody biomass in vessels ranging from 25' to 45' in diameter. By measuring and mapping the material surface in a 70° beam angle, and accounting for irregularities, the device is highly accurate compared to other non-contact devices that only measure a single point.
• Weight and Cable-Based Sensors
Weight and cable-based sensors work extremely well in most solid materials, and are ideal for applications such as pellets or wood chips that flow freely. They work by dropping a weight to the surface of the material and then retracting, much like an automated tape measure. The measurement data is highly accurate, and can be sent to a PLC, control console, or to a PC for monitoring.
Measurements can also be taken in specified time intervals or on-demand. Reliable and affordable, the key to a cable-based sensor’s success is mounting it in the proper location of the tank to account for the angle of repose of the flowing material. Mounting about 1/6th from the outer perimeter of the tank is proven to deliver the greatest accuracy in center-fill, center-discharge vessels.
• Point Level Indicators
Point level indicators send an alert when material in a bin reaches a certain point, and are used to prevent overfilling or running out of material. They are commonly installed in storage tanks, as well as in load-out bins; used near the bottom of a bin to alert when empty, or at the top to alert when full.
A rotary level indicator works by rotating a paddle inside a bin. When material comes into contact with the paddle as the bin is being filled, the turning stops, and an alert is sent to indicate the material has reached the level of the rotary. Conversely, when material falls away from the paddle, and it begins turning again, it’s an indication that material is below the level of the paddle. As a high level indicator, rotaries are mounted on the outer wall, near or on the top of a bin. As a low level indicator, they’re mounted low on the sidewall or in the cone of a bin.
Rotaries work best in free flowing materials, making them ideal for use when measuring pellets and chips. Wood pellets are relatively easy to measure, as they tend to be more consistent in size, are free flowing, and less prone to bridge or rat hole. Rotaries can also be used in sawdust, so long as isn’t moist and rat holes around the paddle. Avoid using rotaries in stringy material such as hog fuel, as it can wrap around the paddle and cause a false signal.
Vibrating rods are also a reliable point level indicator in most wood pellet and wood chip applications, so long as the material flows freely and doesn’t have a high-moisture content. They can also be used in lighter materials, such as with sawdust and shavings. If using a vibrating rod, look for a single-blade design that eliminates the risk of material becoming stuck or giving a false signal, as might occur with a tuning fork design.
Jenny Nielson Christensen, MBA is director of marketing of BinMaster Level Controls.
BinMaster Level Controls
www.binmaster.com
Author: Jenny Nielson Christensen
Volume: November/December 2012